Understanding Automotive Plastic Injection Molds: Revolutionizing the Industry
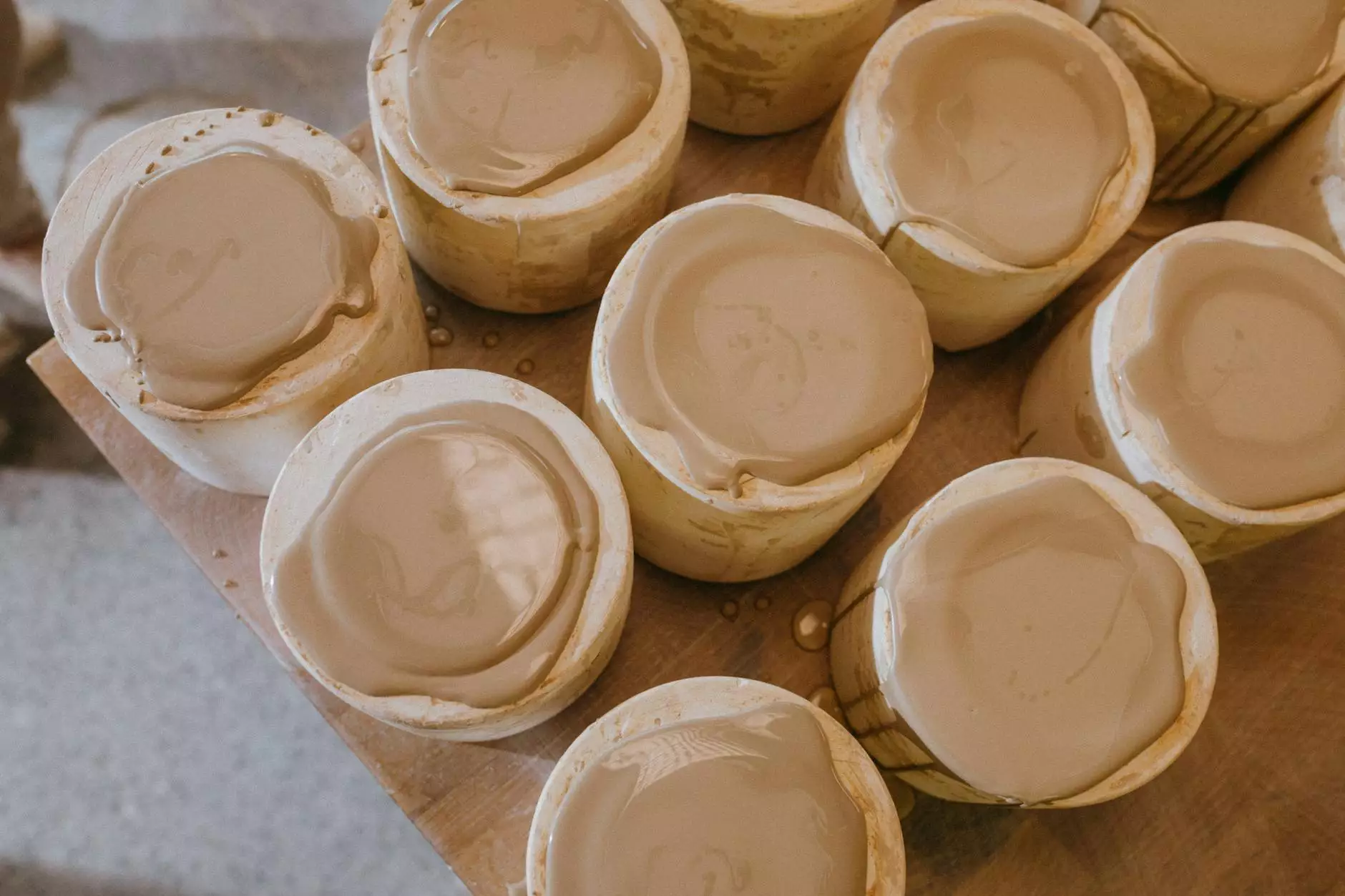
Automotive plastic injection molds are at the forefront of modern manufacturing technologies in the automotive sector. As the demand for lighter, more efficient vehicles rises, the importance of advanced molding techniques cannot be overstated. This article delves deep into the intricacies of automotive plastic injection molds, exploring their benefits, applications, and the future potential of this game-changing technology.
The Basics of Automotive Plastic Injection Molding
To understand the significance of automotive plastic injection molds, it's essential to grasp the basic principles of injection molding itself. Injection molding is a manufacturing process where melted plastic is injected into a mold to form specific shapes. This process is widely favored due to its versatility, efficiency, and ability to produce high volumes of parts with tight tolerances.
How Injection Molding Works
The injection molding process can be broken down into several key stages:
- Material Preparation: The process begins with the selection and preparation of thermoplastic material, typically in pellet form.
- Melting: The pellets are heated until they melt into a viscous liquid.
- Injection: The molten plastic is injected into a precision-engineered mold at high pressure.
- Cooling: The injected plastic cools and solidifies within the mold, taking its shape.
- Ejection: Once cooled, the mold opens, and the newly formed part is ejected.
Why Automotive Manufacturers Prefer Plastic Injection Molding
There are several compelling reasons why automotive plastic injection molds have become a preferred choice for manufacturers:
- Cost Efficiency: While the initial setup costs can be high, injection molding is cost-effective for large production runs due to low per-unit costs.
- Material Versatility: Various materials can be used, including ABS, Polypropylene, and others, which can be selected based on the specific needs of the vehicle components.
- Enhanced Design Flexibility: The ability to create intricate designs with tight tolerances helps manufacturers innovate continuously.
- Weight Reduction: Using plastic components wherever possible contributes to overall vehicle weight reduction, improving fuel efficiency.
- Durability: Automotive plastic parts exhibit excellent durability and resistance to chemicals, heat, and impact.
Key Applications of Automotive Plastic Injection Molds
The versatility of automotive plastic injection molds allows them to be employed in various parts of a vehicle:
1. Interior Components
Plastic injection molding is widely used for manufacturing interior components such as:
- Dashboard Panels: Styled with precise dimensions and varying textures.
- Console Housings: Ergonomically designed for user comfort.
- Door Panels: Customized for aesthetics and functionality.
2. Exterior Components
Lightweight plastic molds are frequently utilized for exterior parts such as:
- Bumpers: Designed for both style and crash safety.
- Grilles: Enhancing the vehicle's frontal appearance.
- Fenders: Offering protection while reducing weight.
3. Engine Components
Even under-the-hood components can benefit from this technology:
- Air Intake Manifolds: Optimizing airflow while being resistant to heat.
- Covers: Protecting sensitive components from external elements.
Innovative Features of Modern Automotive Plastic Injection Molds
The evolution of automotive plastic injection molds has resulted in the incorporation of innovative features that enhance performance:
1. Multi-Cavity Molds
These molds allow for the simultaneous production of multiple parts. This advancement leads to increased efficiency and lower production costs by maximizing mold capacity.
2. Automated Molding Systems
Integration of robotics and automated systems in the injection molding process can enhance precision, reduce labor costs, and improve safety in manufacturing facilities.
3. Eco-Friendly Molding Techniques
Modern automotive manufacturers are increasingly focused on sustainability. Techniques such as using recycled materials and developing bioplastics are becoming more prevalent.
Challenges in Automotive Plastic Injection Molding
Despite its many advantages, several challenges must be addressed:
1. Design Limitations
While design flexibility is a benefit, there are still some limitations. Intricate designs with undercuts may require additional tooling or secondary processes.
2. High Initial Investment
The costs associated with mold design and production can be substantial. However, these costs are mitigated over time through high production volumes.
3. Material Constraints
Selecting the right material is crucial. Not all plastics are suitable for every application, particularly those that experience high temperatures or mechanical stress.
The Future of Automotive Plastic Injection Molding
The future for automotive plastic injection molds is bright, with emerging trends that promise even more innovations:
1. 3D Printing Integration
As 3D printing technology matures, its integration with traditional plastic injection molding processes could lead to rapid prototyping and production efficiencies.
2. Smart Manufacturing
IoT integration and smart factories are paving the way for real-time monitoring and quality control in the injection molding process, enhancing efficiency and reducing waste.
3. Sustainability Efforts
With increasing regulations on environmental impacts, the automotive industry is moving towards eco-friendly materials and production methods. This will not only benefit the environment but also enhance brand reputation.
Partnering with the Right Manufacturer
When considering automotive plastic injection molds, partnering with an experienced and reputable manufacturer is crucial. For businesses in need of high-quality plastic injection molding solutions, Deep Mould stands out in the industry.
Why Choose Deep Mould?
- Expertise: With years of experience in the field, Deep Mould understands the complexities of automotive applications.
- State-of-the-Art Technology: Our advanced tooling techniques ensure precision and quality.
- Customer-Centric Approach: We work closely with our clients to meet their specific needs, ensuring satisfaction and productive partnerships.
Conclusion
In summary, automotive plastic injection molds play a vital role in the automotive industry, driving innovations, cost efficiencies, and sustainability. As manufacturers continue to strive for excellence and adapt to market demands, injection molding technology will undoubtedly evolve, contributing to the future of mobility. For transformative solutions in plastic injection molding, look no further than the expertise offered by Deep Mould.