Understanding Plastic Injection Mold Parts for Your Business Needs
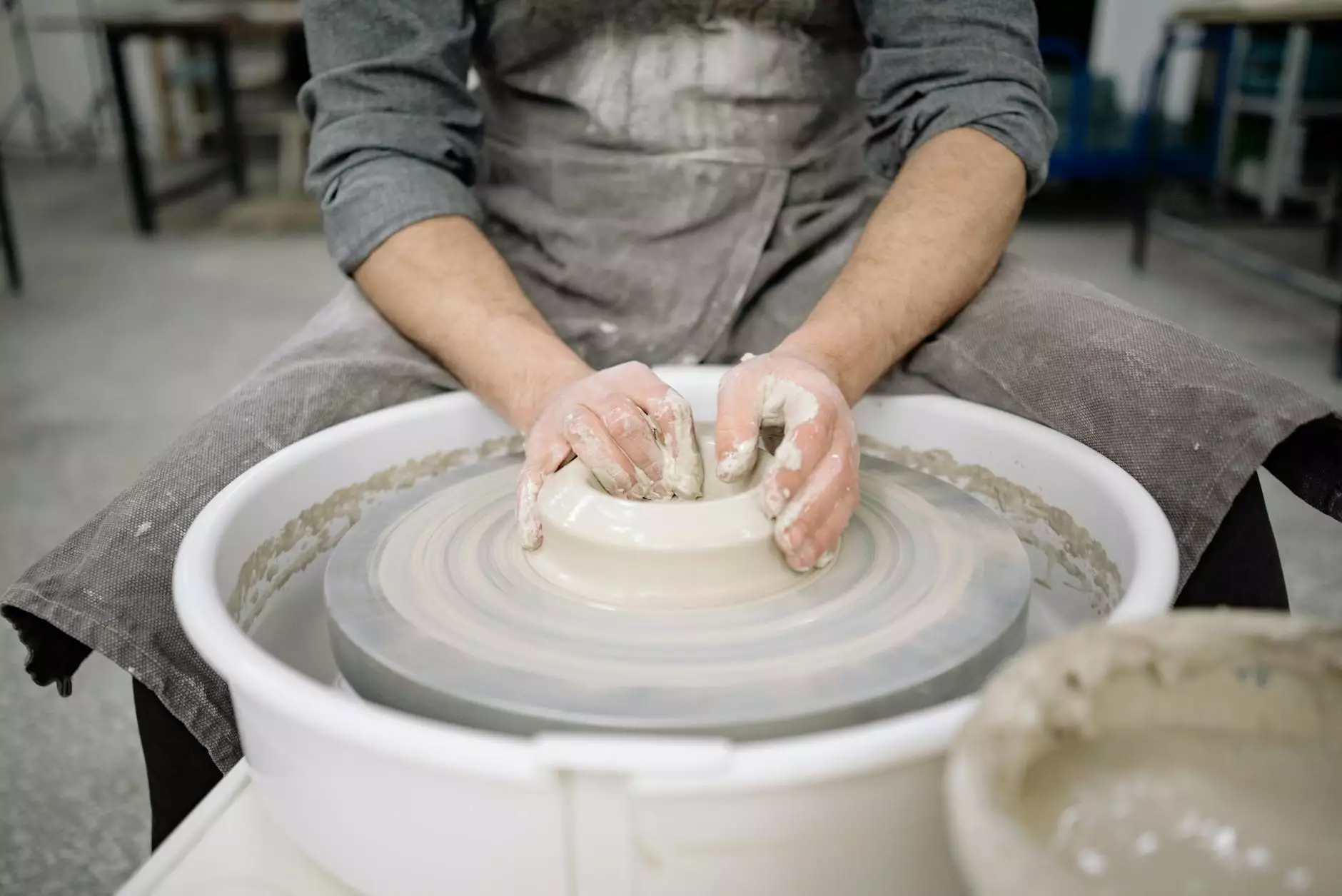
Plastic injection mold parts are crucial components in the manufacturing industry, particularly in factories where efficiency and precision are paramount. These parts not only maximize production rates but also ensure that products meet high standards of quality. In this comprehensive article, we will delve into the world of plastic injection molding, exploring its processes, benefits, and why deepmould.net stands out in this sector.
The Basics of Plastic Injection Molding
Plastic injection molding is a manufacturing process that involves the injection of molten plastic into a mold, where it cools and solidifies into the desired shape. This method is favored for its ability to produce large quantities of parts with precise dimensions and repeatable quality. The process serves various industries including automotive, medical, consumer goods, and electronics.
Key Components of Plastic Injection Molding
- Mold: The mold is a hollowed-out block that defines the shape of the part. It consists of two halves that come together to form the cavity where the plastic is injected.
- Injection Unit: This component melts the plastic pellets and injects the molten material into the mold.
- Clamping Unit: The clamping unit holds the mold closed during the injection process, with sufficient pressure to avoid leaks.
- Cooling System: To allow the molten plastic to solidify, a cooling system circulates coolant, typically water, around the mold.
Benefits of Plastic Injection Mold Parts
The benefits of plastic injection mold parts are manifold, making them an integral part of modern manufacturing:
1. Cost-Efficiency
Once the initial setup is complete, plastic injection molding is very cost-effective for mass production. The ability to create hundreds of thousands of identical parts with little variance allows companies to benefit from economies of scale.
2. Design Flexibility
Manufacturers can create complex geometries and intricate designs with plastic injection mold parts. This flexibility opens up a world of possibilities for product design and innovation.
3. Material Versatility
Plastic injection molding can utilize numerous materials, including various thermoplastics and thermosetting polymers. This versatility means that businesses can choose the best material for their product’s requirements, whether it be strength, appearance, or functionality.
4. Minimal Waste
A significant advantage of the plastic injection molding process is its efficiency in material use. The process produces very little waste compared to other manufacturing techniques, making it an environmentally friendly choice.
5. High Precision and Repeatability
Once set up, plastic injection molds can produce parts to tight tolerances and maintain quality over long production runs. This is critical in industries where precision is paramount, such as within the automotive and medical sectors.
Common Applications of Plastic Injection Mold Parts
Plastic injection mold parts are found in an array of applications across various industries. Here are some key sectors that rely heavily on this manufacturing method:
Automotive Industry
The automotive industry benefits significantly from plastic injection molded parts, which are used for everything from interior panels to intricate components of engines and transmissions. The lightweight nature of plastic also contributes to fuel efficiency.
Consumer Electronics
Devices such as smartphones, laptops, and televisions utilize plastic injection mold parts extensively. These parts not only house essential components but also provide aesthetic value, with customizable designs enhancing visual appeal.
Medical Devices
Many medical applications rely on plastic injection mold parts for producing crucial devices, such as syringes, diagnostic equipment, and other disposables. The ability to maintain high levels of cleanliness and precision is essential in this sector.
Household Goods
Everyday items, from toys to kitchen tools, often derive from plastic injection molded parts. This technique allows for mass production, making consumer goods affordable and widely available.
Choosing the Right Partner for Plastic Injection Mold Parts
When seeking a supplier for your plastic injection mold parts, choosing the right partner is vital to ensuring quality and efficiency. Here are some factors to consider:
1. Experience and Expertise
Look for a business that has a proven track record in manufacturing plastic injection mold parts. This experience not only signifies a familiarity with the process but also suggests the ability to adapt to various requirements and challenges.
2. Technology and Equipment
The supplier should utilize state-of-the-art technology and modern equipment. Advanced machinery can significantly improve production speed and part quality.
3. Quality Assurance
Quality control processes are imperative to maintaining high standards throughout the manufacturing process. A reputable partner should have strict quality assurance measures in place including testing and inspection protocols.
4. Flexibility and Customization
A good partner will be willing to accommodate specific needs and provide customized solutions. Whether you require unique designs or specific materials, flexibility is key.
5. Competitive Pricing
While cost isn’t the only factor, competitive pricing can influence your decision. It's essential to balance quality and price, ensuring you receive value for your investment.
Why Choose DeepMould for Your Plastic Injection Mold Parts?
When it comes to sourcing high-quality plastic injection mold parts, DeepMould is your ideal partner. As a leading provider of metal fabricators, we pride ourselves on offering durable, precision-engineered components that cater to a diverse range of industries. Here are several reasons why businesses consistently choose us:
Unmatched Expertise
With years of industry experience, we understand the nuances of plastic injection molding and are equipped to handle both large and small-scale projects with ease.
Advanced Production Capabilities
Our cutting-edge equipment allows us to produce high-quality plastic injection mold parts efficiently, ensuring rapid turnaround times without compromising quality.
Commitment to Quality
At DeepMould, quality is our cornerstone. We adhere to rigorous testing and quality control measures throughout the production process, guaranteeing that our mold parts meet and exceed industry standards.
Tailored Solutions
We recognize that each client's needs are unique. Our team works closely with you to develop customized solutions that align perfectly with your specifications.
Client-Centric Approach
Our dedication to exceptional customer service has earned us a stellar reputation in the industry. We are here to support you at every step, from the initial consultation to after-sales service.
Conclusion
Investing in plastic injection mold parts is a strategic decision for businesses looking to enhance productivity and product quality. The benefits offered by this manufacturing technique are manifold, and by choosing the right partner, such as DeepMould, you can ensure that your manufacturing processes run smoothly and efficiently. Whether it’s for intricate automotive components, essential medical devices, or consumer goods, plastic injection mold parts will always hold a crucial place in modern production.
For those interested in elevating their manufacturing capabilities, we invite you to contact us at DeepMould for more information about our products and services. Let us help you navigate the exciting possibilities of plastic injection molding!